继火烧水炼丹之后,人们发明了传统的炼丹方法。人们在地下开采出金矿石后,把矿石装进筐里,用绞盘像打水一样把筐子提上来,再用锤子把矿石砸成小块,放在石磨上,磨成粗如玉米面的粉末,然后用水拉,让金砂沉到水底,再用火烧,进行炼丹。
现代黄金生产过程已完全机械化、计算机控制、自动化,根据地质队钻出的矿芯,测试金子在哪一层、多少米以下,然后开采出来。现在用提升井架把矿石从地下几百米处带出来,然后用矿车把矿石送到选矿车间,用破碎机破碎。破碎成小石子的矿石再经皮带走廊送到圆锥磨机和球磨机,磨到玉米面的粗度,进入混合槽。在浮选机中加入黄药和浮选油进行浮选。这种方法不同于过去依靠金的比重的传统炼金法,黄药、浮选油和金发生反应,形成气泡,含金金属粘附在气泡上,把气泡刮出来,烘干后就成了金精矿,金精矿的品位比较高,每吨含金三四十克。 然后将金精矿送入球磨机进一步磨矿,通过进出槽进行最后的冶炼,提取出金、银、铜等各种金属。
1.金矿现场冶炼
20世纪70年代以前,黄金生产处于起步发展阶段,除少数矿山开始采用氰化提金工艺外,矿山就地黄金产量主要来源于砂矿重选得到的自然金和精矿的冶炼,以及混汞提金工艺产生的汞膏的就地冶炼,就地产出的黄金仅占总产量的30%,其中70%的黄金被有色冶炼厂回收。
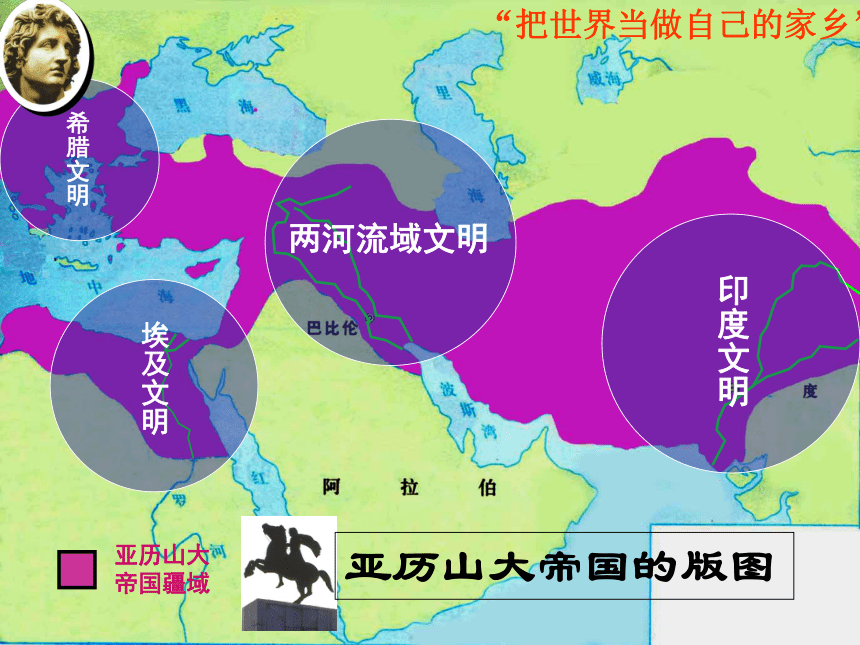
1970年以后,黄金生产逐渐发展,氰化提金工艺日益广泛应用,矿山产金量日益增多,1985年矿山成品金产量占全国黄金产量的70%。选矿厂生产的精矿产品,大部分采用氰化法就地冶炼,生产出成品金。
矿山就地冶炼,大多采用传统的坩埚冶炼法,由于生产工序和加工物料性质不同,产出的金含金量也不同,有的矿山因含金量不高或含银量不高,为提高质量和经济效益,采用化学方法除杂后再冶炼或电解法分离提炼金银。1984年焦家金矿试验采用水冶金新工艺,用电解氯化法(用水溶液氯化法提取金,用氨浸出法提取银)除去氰化金泥中的贱金属,得到金品位为99.9%的成品金和含银量为99.9%的银锭。金泥中的铜和铅也同时被回收(用湿法处理金泥有推广的趋势)。 招远金矿成功研制出φ1.5×1.8m转炉冶炼金泥,取代了以前的坩埚冶炼,降低了成本,改善了劳动条件,该方法已在部分金矿推广应用,效果良好。
2.有色金属冶炼厂伴生金的回收
在黄金生产中,从多金属矿中回收伴生金占有相当大的地位。金与铜、铅等有色金属一起被选入精矿中。在铜、铅的冶炼中,又回收金、银。为了增加黄金产量,全国一些有色冶炼企业相继建成了综合贵金属回收车间,伴生金的产量占全国伴生金总产量的90%以上,是我国黄金生产的一支重要力量。这些企业回收伴生金的依据是在铜、铅冶炼过程中,金、银富集在粗铜、粗铅中。在粗铜、粗铅电解精炼时,金、银沉积在电解阳极泥中。因此,从阳极泥中提取金、银是回收伴生金、银的主要途径。
标题:古代采金方法的演变与现代黄金生产的机械化
链接:https://www.373wan.com/news/xydt/8856.html
版权:文章转载自网络,如有侵权,请联系删除!